Challenges
The rising demand for air travel has led to a 34% increase in direct CO2 emissions worldwide over the past five years. This is expected to further increase by 3-5 % per year as the population grows. Aviation is forecast to be responsible for 24% of global emissions by 2050. As a result, the aviation industry must shift to new, low-carbon propulsion technologies and/or new fuels, such as hydrogen (H2).
The EU has identified H2 as a clean fuel. As such, H2 can help tackle climate change and reduce GHG emissions in a sector as important as aviation. Today’s industry, however, can’t move toward hydrogen-powered aircraft. The main challenge is the absence of viable H2 storage systems in aircraft, considering the strict limitations in weight, volume and cost-efficiency.
Hydrogen’s gravimetric energy density (GED) is three times greater than that of kerosene. This means aircraft would have to be redesigned to allow for larger tanks on board. The size and weight of H2 tanks pose major limitations for high energy demand on flights, thus reducing cost-effectiveness significantly for medium to long-range aircraft.
To respond to these needs, the OVERLEAF project will develop a disruptive low-pressure liquid H2 storage system (LPH) design, combining innovative functional and high-performance materials, thermal insulating materials and novel hydrogen leak detection sensors.
Our innovation
The low-pressure, liquid hydrogen storage system architecture (LPH) will combine new materials solutions, advanced and flexible manufacturing technologies, and sensors into an optimum configuration design. The aim is to improve the thermal performance of the storage tank, minimise the pressure inside the inner and the outer tanks and significantly reduce hydrogen leakage during in-service operation compared to SoA available LH2 storage solutions.
The new LPH storage system will be designed to reach an average gravimetric index (GI) of 40% and overall higher operation flexibility, with an estimated 60% reduction of the total weight/energy consumption and a 25% increase in onboard H2 storage capacities. Thanks to the low operating pressures (maximum 6 bar inside the tanks) that will be attained within the system, it will be possible to propose new composite-based materials solutions and advanced automated manufacturing processes. This will significantly reduce the overall system’s weight, thus, increasing GI. In addition, it will improve the design flexibility of the tanks and their robustness as they are structurally part of the fuselage. Costs will thus be significantly reduced for commercial aircraft compared to state-of-the-art available H2 storage systems.
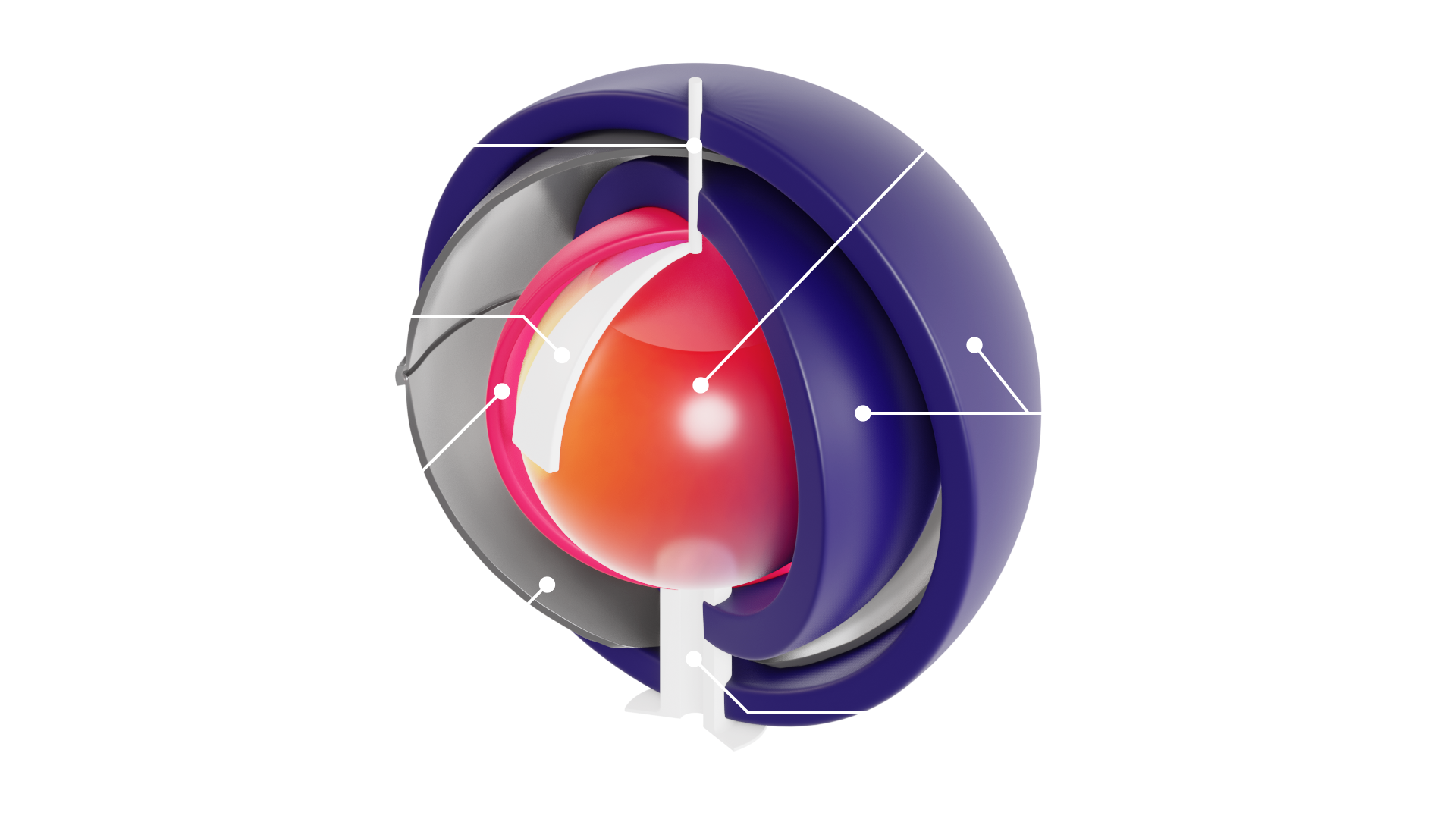